Adhesives
By ROBERT H. GILLESPIE and BRYAN H. RIVER
Forest Products Laboratory1
Forest Service, U.S. Department of Agriculture
ELASTOMERIC ADHESIVES IN BUILDING CONSTRUCTION
Elastomeric construction adhesives: What are they? An adhesive is a substance capable of hold ing materials together by surface attachment. This is a universally accepted definition found in ASTM D-907. But what is an elastomer? What do we mean by " construction?" Efforts to describe adhe sives in terms of properties or uses can be very misleading. Better descriptive terms, a better un derstanding of definitions, and better means of communicating among ourselves and with users and consumers of adhesives are needed.
The term " construction" as a noun means a structure put together from pieces. Construction adhesive suggests an adhesive for use in construc tion and implies universal application. This is certainly overstating the case. An adhesive satis factory for installation of decorative wall paneling may not perform adequately in a roof or floor panel. Proper selection of an adhesive will depend upon the nature of the intended use.
An elastomer is, according to the 1973 edition of D-907, a macromolecular material which at room temperature is capable of recovering sub stantially in size and shape after removal of a deforming force. Does this mean, then, that an elastomeric adhesive is highly elastic? Not neces sarily. All it means is the base polymer used to formulate the adhesive might be classed as an elastomer. The formulated adhesive may be rela tively inelastic. So the definitions are inexact. In frustration it has been suggested that these mate rials be called "elastomer-based extrudable mastic adhesives," but obviously this will not catch on. It is too much of a mouthful and it has no promo tional oomph; thus, the term elastomeric construction adhesives will have to prevail until something better comes along.
Composition
Elastomeric construction adhesives can contain a number of different ingredients with the elastomer making up 30 to 50 percent of the weight of the total composition. These ingredients can include tackifiers or resins, fillers, extenders, plasticizers and softeners, antioxidants, curing agents, seques tering agents, and solvents or dispersing agents. Each of the ingredients adds some needed property to the adhesive system. From essentially the same ingredients, but possibly different proportions, it is possible to make a contact cement with a viscosity range of 1,000 to 30,000 cps. or an extrudable mastic of a more viscous character, something in the order of 80,000 to 800,000 cps. Cements are applied principally by spraying or spreading, while mastics are extruded through a nozzle. It is mainly the extrudable mastic-type adhesives that will be discussed below; however, much of the material presented can be applied to other adhesive systems as well.
Outlook
Extensive use of adhesives in building construc tion is just now beginning to develop. Most adhesive manufacturers and raw material manufacturers are looking to the building industry as a potential volume outlet for their products. Rapid develop- ment of these markets, however, is hampered by a variety of constraints including code restrictions, union attitudes, traditions in building construct ion and consumer preference and lack of knowledge and understanding about the benefits of adhesive technology.
But there are many indications that this situation is changing. Codes based upon performance, given a strong impetus by the HUD Breakthrough pro- gram, are appearing and innovations are more readily accepted by both the builder and the con- sumer. With change occurring in almost every- thing, the housing and building industries will be no exception. Look at the rapid growth of the mobile home and the factory-built home industries. Here is where adhesive bonding has the greatest opportunity for savings and improved performance, because bonding conditions can be more closely controlled in factories than during on-site construc- tion. Possibly the fastest growth in adhesive use in building construction will be in the factory-built area, but extension into on-site building is logical if adequate bonding controls can be imposed.
Nature of Adhesive Uses
Growth of adhesive use will depend to a great extent on how rapidly information can be devel- oped to permit their use in the more critical areas where the adhesive must contribute to load- carrying capacity. The nature of adhesive use can be divided into five different categories; these are, in decreasing order of structural performance requirements: (1) prime structure, adding strength and stiffness; (2) semi-structural component, add- ing stiffness; (3) improving over-the-road resist- ance; (4) field assembly and (5) accessory and trim attachment.
Most critical use is in the prime structure where adhesives will add strength and stiffness through- out the service life. Next most critical is semi- structural use, primarily adding stiffness rather than strength. Critical, but for only short periods, is the need to improve over-the-road resistance during the transportation of panels, modular structures or factory-built homes. Both stiffness and strength are important during transportation because loadings are dynamic and energy absorption is critical.
A new dimension is added with field assembly of modular units. Here long-time permanence is needed but it is possible to remedy weak spots before they become problems. Least critical of the five is use for accessory and trim attachment, some- times termed cosmetic applications. Replacement through redecoration is expected and can be per- formed without detriment to the structure.
Adhesives are already widely used in the last category- fotrim and accessory attachment. They are used for wall coverings, floor coverings, sink and counter tops, roof coverings, ceiling materials and insulation attachment. These applications in- volve a wide variety of different materials as adher- ends including wood, wood-based materials, plas- tics, metals, ceramics and glass in a range of differ- ent shapes and compositions. Elastomeric mastic- type adhesives are already being used in many of these applications.
Adhesives in Structural Applications
The problem, then, is to learn how elastomeric adhesives can be used for the more critical appli- cations where the adhesive must function as an engineering material capable of supporting loads. Here life safety may be a major factor. In other cases, failure could result in no human danger but may destroy the utility of the structure because repair costs would be impossibly high.
The question is why cannot the more conven- tional adhesives be used for these structural appli- cations? The fact of the matter is that they often can. When properly used, the conventional adhe- sives provide thin gluelines that have high strength, high shear modulus. The cured adhesives are hard and tough, effectively transfer stresses from one adherend to another and essentially restrain adher- end movement due to moisture changes. But they have their limitations, too. They have poor gap- filling properties and usually require freshly pre- pared, well-fitted joints for producing quality bonds. Many require special mixing, tight control of bonding conditions, excessive clamping time or special curing conditions and, thus, do not lend themselves very well to the requirements of build- ing construction.
In contrast, the elastomeric adhesives are gap filling and can be used in poorly fitted joints to bond adherends without special surface prepara- tion. How forgiving these adhesives are to surface contamination, however, is still open to question. They have low to medium strength and modulus, are viscoelastic and can creep under excessive loads. They may develop strength rather slowly and require mechanical fasteners to maintain in- tact gluelines while the adhesive sets. Rather than restraining adherend movement with moisture changes, they may conform with the movement and may even relieve the internal stresses that develop within the joints which may be detrimen- tal to their load-carrying capacity. A great deal of research will be needed to determine how well these adhesives can perform in structural or semi- structural applications.
Elastomeric construction adhesives are available today with organic solvent vehicles (these are the most common), such as water emulsions or disper- sions, or without a vehicle and having 100 percent total solids. One of the most attractive advantages of these adhesives is the fact that no mixing or preparation is required, and, in this regard, they are similar to the polyvinyl emulsions or “white” glues which are so readily applied by squeeze bot- tles at a moment’s notice. This is a great advantage but only if the resulting gluelines have respectable long-time performance characteristics.
long-Term Performance
For structural and semistructural application, long-term performance, the ability of an adhesive to hold adherends together under the service envi- ronments typical for the structure and for its full lifetime, is a must. To do this,. an adhesive must resist both chemical and physical types of deterior- ation. Long-term performance is synonymous with durability, but the former term is preferred since it implies that an adhesive joint must perform a func- tion while it is enduring. The term emphasizes that physical forces are at work while chemical-type deterioration takes place at some rate peculiar to the material and the environment.
Deteriorating Influence
These two types of deterioration can be further categorized. The chemical types of influences in- clude the effects of heat and chemicals. Moisture is the most important of the chemicals since it is present to various degrees in all service environ- ments. At high moisture contents, micro-organisms may deteriorate the glue line either by using it as a food source or by generating chemical substances that attack the adhesive or the bond. Other chemi- cal effects that may be important include the cata- lysts or other ingredients in the adhesive, extrac- tives, fire-retardant and preservative treatments, metallic ions from metal adherends, oxygen from the air or air pollutants. Any or all of these may
require special evaluation.
The physical influences on gluelines may also be
subdivided. There are the internal stresses that take place when adherends change dimensions due to moisture or temperature changes. Then there are the externally applied loads imposed by the structure either as continuous dead loads or as short-term live loads.
For an adhesive to be used with confidence for structural applications, information is needed on how it responds to these deteriorating influences that determine long-term performance. Just how this information should be collected, what tests should be used and how the information can be translated into useful design data is a big question. This question will never be completely answered for their is need for continual research for better test methods, more accurate predictions and more precise methods of design.
As a start toward progress in this very complex field, the Forest Products Laboratory (FPL) put together a report entitled “Evaluating Adhesives for Building Construction.” 1 This report represents an attempt to recommend suitable test procedures and needs for new procedures to answer the perti- nent questions about adhesive use in building construction.
Chemical Types of Influences
Probably the greatest need for test method de- velopment has to do with the chemical types of deterioration that affect adhesive bonds. Over the years, many accelerated tests have been devised on an empirical basis, hoping for some correlation with service experience.
The futility of using empirical methods to predict an adhesive’s service life was recognized several years ago at the Forest Products Laboratory, and a new approach was devised. This approach is called the rate-process method because its purpose is to determine how fast bond strength is lost under carefully controlled conditions in the laboratory. The exposure conditions are carefully selected so that the effect of temperature change, or changes in moisture or other chemical concentration, is determined; how fast bond strength is lost under any temperture or moisture condition can then be estimated and this information can then be tied in to any service environment whose climate can be defined by its temperature and mosture situation.
In using the rate-process method for forecasting many specimens, essentially lap-shear specimens, are exposed to controlled temperatures and peri- odically a set is removed for strength tests. Fig- ure 1 illustrates the results for an elastomeric con- struction adhesive where the shear strength is plotted as a logarithmic function versus time to give a least squares regression line for each ex- posure temperature. From this, the time for half the shear strength to be lost in each case is ob- tained. The logarithm of this half-life is then plotted against the reciprocal of the absolute tem- perature. If the work is done carefully, it is amazing how well the data fit the straight-line, temperature- dependent relationship proposed by Arrhenius many, many years ago and further defined by Eyring and co-workers more recently. Figure 2 shows how at 27°C (80°F), adhesive A would resist thermal degradation for 1,600 years and ad- hesive K for 350 years.
This method of forecasting involves extensive extrapolation outside the range of the experimental conditions used- somethingeveryone was taught not to do. But the challenge is for someone to come up with a better method of forecasting to 50 years and beyond with a system that has any better scientific validity. This proposed system not only forecasts life expectancy but helps pinpoint the cause of degradation.
The work done toward developing this rate- process method was first reported in articles in 19652 and in 19683. These articles describe the basic principles of rate-process methods as used to evaluate some representative wood adhesives but do not extrapolate for forecasting purposes. These results were so encouraging that the method was used to evaluate elastomeric construction ad- hesives to see if the methods would be useful with this entirely different class of adhesives; these results were reported by River 4 at the annual meet- ing of the Forest Products Research Society in Dallas, Texas, June 1972.
Rate-Process Method in Action
In this study representative commercial adhe- sives of four polymer types, a polyurethane, neo- prene, styrene-butadiene and reclaimed rubber, were evaluated. The polyurethane was 100 percent solids and cured by moisture activation. The others were solvent systems ranging from 53 to 70 percent solids.
Two types of specimen were used. First was a two-ply yellow birch lap-shear specimen, which is essentially a plywood lap-shear specimen without the core. The face plies are oriented with the grain direction parallel to the line of force used in test- ing. These specimens were pulled in tension.
The second was a ponderosa pine tensile- splitting specimen which is essentially the same as that described by Strickler,5 but with the grain angle oriented toward the glueline as suggested by Stanger and Blomquist.6 These were pulled in ten- sion to cause the specimen to split along the glue- line. They were used only for dry-heat exposure.
These two specimens represent the two most important stress conditions that must be consid- ered for gluelines in building applications- shear along the glueline and tension perpendicular to it. The specific specimens were selected because of the importance of these stress conditions to design engineers. The exposures used included water soaking, moist heat with 15 percent wood moisture content and dry heat. At least three exposure tem- peratures were used in each case.
Original Strength Properties
The original strength of the adhesive bonds pre- sented in Figure 3 was obtained by testing 20 of the cured specimens before exposure. The middle horizontal line on each of the bars indicates the mean value, with the top and bottom lines of a bar indicating the 95 percent confidence limits about the mean. The length of the bars gives an indica- tion of the variability in the test results. The strength values for the lap-shear specimens are in kilopascals. If these values are divided by 7, the approximate value in pounds per square inch is obtained. The strength values for tensile-splitting specimens are in Newtons per centimeter of width.
Unexposed lap-shear specimens bonded with neoprene (C) and styrene butadiene (E) were origi- nally twice as strong in shear as those bonded with polyurethane (A) and reclaimed rubber (K). Vari- ability was very low with polyurethane due to the nature of the adhesive, i.e., 100 percent solids and the fact that failure was entirely within the adhe- sive. Neoprene, although of high strength, gave highly variable results due to the variable honey- comb structure of the cured adhesive and also sporadic wood failure rather than adhesive failure.
Tensile-splitting test results on the right-hand side show polyurethane almost twice as strong as the other adhesives when tested in a tensile mode. The higher strength of polyurethane in this type of specimen results from its higher degree of flexibil- ity. So the initial strength and variability of the joint depend both on the properties of the adhe- sive and the way it is tested.
Strength lost During Exposure
In using the method, during the exposure of specimens to elevated temperatures and controlled moisture content a set of five specimens is re- moved after each of a number of exposure times. These specimens are tested for strength, the values averaged and the 95 percent confidence limits about the mean are calculated. When each ex- posure is complete, there are eight data points to establish the degradation rate at each set of condi- tions. Figure 4 is a typical degradation rate plot showing bond strength in kilopascals on a logarith- mic scale versus time of exposure in days The mean data points are closely situated about the least squares regression line The slope of the line is the degradation rate. In this case, the time to half-strength is indicated as 7.5 days
The same data, but with the addition of the 95 percent confidence limits about the mean added as vertical lines through the data points, are given in Figure 5. This gives a picture of the variabilily and change in variability as exposure progresses These results show uniformly low variability throughout this particular exposure for this adhe- sive and also that strength decreased at a uniform rate throughout the exposure. This is the kind of result expected and preferable, but all adhesives, and especially the elastomeric, do not behave in such a nice clean-cut fashion
For example, Figure 6 shows a rate-loss curve that changes during the time of exposure. It differs from the previous results only in the temperature of exposure. Initially the degradation rate was very fast, making the time to half-strength very short, about 2 days. But shortly afterward, at about 3 days, the rate slowed so that applicable strength was retained for a long period of time. If the service-life criteria had been 300 kP, instead of half the original strength, one can see that the results would have been much different in time. So sometimes the time to half-strength does not adequately describe the behavior of the adhesive. Again, characteristic of adhesive A lap-shear joints, variability is low and quite uniform.
In contrast, high variability appears to character- izeoneoftheotheradhesives(Fig.7). Inthismoist heat exposure, the variability seems to decrease with exposure time. The apparent reason for this behavior may be an increasing percentage and uni- formity of wood failure rather than adhesive failure at the longer exposure times. This suggests that the wood is degrading faster than the adhesive in this case.
In other cases, high variability occurs through- out the exposure period (Fig.8). A reasonably straight line relationship exists except for a large drop and recovery of strength in the very early stage of exposure. So here again, depending upon which part of the curve one chooses, the time to half-strength could be as long as 20 days or as short as about 1 day.
These examples show differences in behavior, characteristic of certain adhesive-exposure interac- tions, which make it difficult to apply the rate- process methods to forecast service life with the degree of accuracy one would like. But each of the rate curves supplies some important information about how an adhesive behaves in a particular environment and adds to the overall picture of its anticipated performance. In the case of the polyurethane, the time to reach half the original strength was obtained from each of the rate curves. These times were then plotted according to the Arrhenius temperature-dependence relationship to yield the data shown in Figure 9.
Rate Changes With Temperature
For comparison purposes, values for wood for dry heat and wood for water soak are included. These data were obtained from earlier work with plywood specimens bonded with phenolic adhe- sives which were more durable than the wood. When tested, these specimens failed in rolling shear in wood, indicating the degradation rates and tem- perature dependence observed were for wood it- self. The lines for polyurethane are all quite parallel but as a group have steeper slopes than the lines for wood. This means that the temperature sensitivity of the adhesive's degradation rate is not influenced by moisture concentration, but that as a group the adhesive's rates are more temperature sensitive than the wood's. Time to half-strength is shorter than for wood at elevated temperatures, but be- cause of the differences in slopes of the lines, extrapolated service life of the adhesive is compar- able to wood at normal temperatures. Because the data obtained for polyurethane were so consistent, forecasts of its service life were made.
At 27°C (80°F), the polyurethane can be ex- pected to last for 20 years in the most severe exposure, water soaking. However, at 70°C (158°F), which can occur in roofs, expected service life is only about 880 days. How significant this is de- pends upon where service is to take place, and on the judgment of the design engineer viewing his particular design as to whether or not this adhesive can be used in roof construction with reasonable safety.
Neoprene has an excellent reputation a5 a dura- ble elastomer when properly compounded. The ex- ample evaluated has a tight envelope of Arrhenius lines, showing excellent resistance to moisture (Figure10). These lines are also bracketed by the lines shown for wood. The temperature sensitivity is about the same as wood. One exception is the behavior in moist heat, but that line is subject to revision with additional data. Joints bonded with neoprene are somewhat more affected by dry heat than is wood but behave about the same as wood in water soaking. On the basis of these particular tests, it appears that neoprene should be as durable as wood.
The styrene-butadiene and reclaimed rubber- based adhesives were quite variable in strength and produced rate-loss curves during exposure that were not clear cut and easily interpreted. One very important point- thefour adhesives evaluated in the study were rather arbitrarily selected; their results should not be interpreted as representing all adhesives of the types mentioned.
Effect of Oxygen
Another phase of the study compared the effect of dry heat in air and also in pure oxygen atmos- pheres because elastomers are subject to oxidation. Data on oxygen aging were obtained with the help of some industry friends who were kind enough to remove specimens from their oxygen bomb peri- odically so a rate curve could be obtained, but since standard oxygen bomb equipment is run only at 70°C it was not possible to obtain an estimate of the temperature dependence of these joints in oxygen. In all likelihood, the temperature depend- ence would be similar to that obtained for dry heat, for the only difference is in the concentration of oxygen.
Figure 11 shows the Arrhenius temperature- dependent lines for wood and both lap-shear and tensile-splitting specimens in dry air. The single points at 70°C are the time to half-strength for both types of specimens in oxygen. Polyurethane shows a great difference between the two kinds of speci- mens in air aging. Although the temperature de- pendence is about the same, the tensile-splitting
joints are less durable than the lap-shear joints at a given temperature. Both joint types are less dura- ble than wood. Tensile-splitting joints in air most nearly approximate the durability of joints exposed to oxygen atmosphere. The time to half-strength in oxygen is nearly the same for both kinds of specimens. Polyurethane does have some sensitiv- ity to oxygen, but it does not appear to be great. These results demonstrate how the oxygen bomb test can be used to relate to the rate-process method of evaluating chemical types of deterioration.
The development of these rate-process methods of forecasting resistance to chemical types of de- terioration is continuing at the Forest Products Laboratory, current efforts focus on increasing the accuracy of prediction and assessing the statistical significance of the results. Accuracy is highly de- pendent upon decreasing the variability in strength of the bonded joints. With some of the elastomeric construction adhesives, this variability is very high. It has been rationalized that this is due to the honeycomb structure that develops within the adhesive as it loses solvent in the glueline. When bubbles with thin walls are formed, the strength is low. Thick-walled bubbles provide higher strength. The lack of control over the way solvent is lost leads to high variability in the strength developed. This variability in strength certainly must affect performance in service. There is no question that it adversely influences the prediction of service life and in providing useful values for use by design engineers. The variability of joint strength devel- oped by elastomeric construction adhesives must be reduced and their oxidation resistance main- tained or improved if they are to find extensive use in structural applications.
Science Environments
The results of both the chemical resistance tests and the mechanical property measurements must be capable of translation to the expected service conditions. This temperture scale (Fig. 12) sum- marizes the expected range of temperatures found in houses. The maximum temperatures are of greatest interest. In roof sections, maximum tem- peratures as high as 160°F are not uncommon. Outside walls may reach 120°F. Floors are usually in a narrow range of 60 to 90°F. The temperatures used in accelerated aging range from 140 to over 290°F, so it is necessary to extrapolate the results back to the service temperature range.
When measuring the mechanical properties of adhesive-bonded joints and determining the effect of loads, the effect of various service conditions also must be considered; however, the measure- ments can be made in the actual temperature range of interest. To be all-inclusive, measurements should be made at 80, 120, and 160°F, both wet and dry. The dry tests would simulate normal conditions in floors, sidewalls or roofs. The wet tests would reflect adverse conditions such as leaks in roofs, moisture condensation in sidewalls and roofs or flooding of floors by plumbing leaks. The object is to collect data on an adhesive so the design engineer can select the most appropriate data for each specific design requirement.
Physical Phenomena
Besides resisting chemical types of deterioration, an adhesive must also resist the forces imposed on the joint in service. These internal stresses arise from dimensional changes that the adherends undergo with changing environment as well as the external loads imposed on the joint as part of a structure.
Internal-Stress Development
The internal-stress development has been diffi- cult to measure in a quantitative sense. The usual way is to subject specimens to some exaggerated cyclic exposure and measure how much strength might be lost. When such tests are applied to joints bonded with elastomeric construction adhe- sives, the best ones show little if any loss in strength. This verifies the supposition that these adhesives are capable of relieving internal stresses whenever they develop. In fact, it has been pro- posed that this property of elastomeric adhesives be put to work to actually relieve stress in joints and maintain high strength. Krueger and Blomquist explored this possibility in the 1960s with encouraging results. Krueger's initial work was with an epoxy polysulfide formulated to match the shear modulus of the wood used for adherends. He later extended the work to include adhesives of lower modulus in thick gluelines, 8 again with success. He developed a method for measuring the shear mod- ulus of adhesives in joints9,10 since the prediction of performance depended upon reasonably accurate values for this mechanical property.
It is interesting to compare materials on the basis of their shear modulus:
Material
Douglas-fir (radial-tangential plane)
Phenol-resorcinol
Polyvinyl acetate
Epoxy-polysulfide (30-70)
Elastomer (Krueger)
Commercial elastomeric construction
Shear modulus (psi)
13,000
135,000
50,000
15,000
135
50-9,000
Note that coast-type Douglas-fir has a shear mod- ulus of 13,000 psi in the radial-tangential plane where the maximum swelling strain takes place. A conventional phenol-resorcinol has a modulus about 10 times greater than Douglas-fir while a polyvinyl acetate is 3 to 4 times more rigid. The epoxy-polysulfide adhesive used by Krueger had a shear modulus of 15,000 psi while the elastomer used later was only one-tenth as rigid.
Recently at the FPL, the shear modulus of a number of representative commercial elastomeric construction adhesives was measured using a simplified method involving parallel plates strained in shear, The time-honored torsion method also has been used. The values obtained for elastomeric construction adhesives ranged from 50 to 9,000 psi, well below that of wood but still covering a broad range. What this means is that elastomeric con- struction adhesives are available or can be formu- lated to provide a range of shear modulus values and that design engineers have an opportunity to make use of this property in designing specific structures.
Kuenzi and Wilkinson11 used shear modulus values for adhesives to develop an analysis capable of predicting the deflection and stresses for com- posite beams bonded with elastomeric adhesives; other work in this field has been carried out by Hoyle12 and these are only examples. The signifi- cance of this is that engineers already are develop- ing methods for predicting the performance of structures or components of structures bonded with elastomeric adhesives.
These adhesives provide only partial interaction between built-up pieces because the adhesives are less rigid than the components. The investigators looked at the deflection and strength of composite beams rigidly bonded together with a conventional adhesive to provide complete interaction and com- pared this with the deflection and strength of the same built-up members without any interaction- in other words, without any fastening at all. They then developed an analysis that would take into account partial interaction as provided by nails or by mastic adhesives. This resulted in methods for rational design of various composites that de- pended upon a knowledge of the properties of the components including fastener rigidity.
Fastener rigidity variables had not been consid- ered heretofore. This allowed for a wider choice of materials for more efficient designs of structural components, even for possible fabrication at the building site. But these methods have to be learned and applied by design engineers, and this is an- other communication problem in transposing re- search results into practice.
An alternative predicting composite behavior from component properties is the more common practice of building full-scale prototypes and test- ing for deflection and strength under the antici- pated service environment. This is expensive and requires large-scale testing facilities. So there is need for additional engineering research for the development of accurate predictive methods using material property data.
In this regard, there appears to be controversy about what data to use when both mechanical fas- teners and adhesives are used in the fastener sys- tems. Many proposals involve nail-gluing with elastomeric construction adhesives. Which fastener should be considered as controlling the deflection and strength of the composite? Research is needed to resolve the problem of assessing the contribu- tion of each fastener type when combinations are used. But engineers need factul data on the me- chanical properties of adhesives to make predic- tions with accuracy. This represents just the beginning of efforts by design engineers to select material for composites on the basis of particular properties so that the performance of a structure can be predicted, controlled and maximized.
Externally applied loads
Adhesive joints in structural applications usually are required to carry some externally applied loads. How much load and for how long a time the joint can carry a load is a matter requiring measurement. This is usually done by applying a dead load to an adhesive joint in shear and determining the time that elapses before the joint breaks. The applied loads should be selected fractions of the values obtained on the universal testing machine for test- ing the same adhesives in rupture times of 1 to 3 minutes.
An example of the kind of useful data that can be obtained in this way is shown in Figure 13. In this case it is a composite for three species of soft- woods. This shows that a continuous application of 60 percent of the load required to break the specimens on a universal testing machine in 3 to 5 minutes would result in rupture in 50 years.
Theory as well as experiment says that the load required for rupture of visco-elastic materials is a linear function of the logarithm of time. Some tests of this type have been performed on elas- tomeric construction adhesives. Figure 14 shows the results of evaluating a relatively high-strength adhesive for rupture stress as a function of time covering the span from 0.1 hour to 10,000 hours, which is over a year. The top lines show the re- sponse at room-temperature conditions and the bottom line, at high temperature and moisture, the most rugged conditions the adhesive might meet.
At room temperature, a high initial rupture stress of over 1,400 psi declines to about 520 psi in the time span shown here.
The straight-line equations produced from data such as these can be used to calculate rupture stress expected at any time with estimates made for periods of time of 1, 10 or up to 100 years. Table 1 compares two adhesives for estimates of duration of load at room conditions.
The short-term rupture stress is that obtained with a universal testing machine in 1 to 3 minutes. The predicted rupture stress for the more rigid adhesive is 530 psi at 1 year and 150 psi at 100 years; for the less rigid adhesive, 240 psi and 175 psi for the same time periods. Both would probably he suitable for applications in moderate temperature and moisture conditions.
But at high temperature and moisture conditions, the less rigid adhesive would fail at less than 50 psi before 1 year while the more rigid adhesive would still support a stress of 150 psi for as long as 100 years. Under these conditions, the more rigid ad- hesive would be expected to perform much more satisfactorily than the less rigid elastomer. Data of this type can usually be collected in about 1 to 2 months to give reasonably safe extrapolations to 10, 50 or 100 years because of the logarithm-time relationship.

Data of this type can in some cases be of con- siderable concern until it is realized that design stresses are usually quite low in many applications. The rolling shear strength of plywood which often governs design is only about 50 psi so there is a place for adhesives with lower unit strengths than conventional types; however, because the lower strength of the adhesives rather than that of the adherends will govern the ultimate performance of a composite, accurate measurement of adhesive mechanical properties is a must. This adds a whole new dimension to the problem of designing and using composites in structures.
When an adhesive joint is under a continuous dead load, it will creep. Unfortunately, this is one of the questionable properties of elastomeric con- struction adhesives. They are often more viscous than elastic. When stress rupture measurements are made under dead loads, bonded joints deform, with the deformation progressing through all stages of creep characteristic of the adhesive. Stress rup- ture measurements tell how long it takes for the entire creep process to take place, but they do not provide any information as to how much deforma- tion has occurred.
The measurement of creep properties under the various service environments and how these meas- urements can be interpreted for engineering design use is a matter of question. There is an urgent need for new and better methods of measurement. While it is a subject that cannot be dealt with in depth here, it certainly deserves more thorough treatment.
Other Important Properties
Other properties of elastomeric construction ad- hesives are also important in their use in building construction. For example, how do they behave in fire situations? Do they soften or melt and allow the structure to collapse or do they maintain suffi- cient strength for the building to remain intact until occupants can safely leave the structure? Tests are being conducted in this area but are still too incomplete to be discussed here. Another impor- tant consideration is how well elastomeric con- struction adhesives behave for acoustic damping purposes? With noise pollution being of current concern, elastomeric construction adhesives might well find use as decouplers and damping materials to reduce noise transmission through walls. This would take advantage of a special property of elas- tomeric adhesives but would be in no sense a structural application.
Design Stresses
For structural applications, design engineers make use of a variety of systems for calculatingdesign stresses. One approach is suggested by the way design stresses are assigned for wood. Values for the mechanical properties of clear wood speci- mens which can be found in ASTM D2555 are con- verted into design values by a series of factors that adjust the ideal situation to that of a real life situ- ation. Ifthisanalogyisappliedtoanadhesivejoint using shear stress as an example, an equation like the following would develop the design stress:
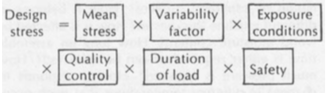
The mean stress value, obtained from standard test procedures, would yield a design stress value after adjustment by a series of factors. These factors would be concerned with such variables in the system as the variability inherent in the measured strength values, what exposure conditions are to be met, how much quality control will be exer- cised, what is the duration of load that can be expected and, possibly, how much factor of safety does one desire.
There might even be another factor added to such a picture, the one having to do with resistance to chemical-type deterioration. A consideration of this approach to calculated design stresses can be very valuable to an adhesive formulator. It tells him that the average or mean stress of the joints produced by his adhesive might possibly be higher. Or he might attempt to reduce the variability in strength that is inherent in his particular system. He may wish to improve its resistance to high tem- peratures or to high moisture contents.
For the quality control factor, he may wish to improve the strength in thick gluelines or in how well it bonds to contaminated wood surfaces or other surfaces. For the duration-of-load factor, he may wish to produce a more elastic type of resist- ance to load rather than produce a viscous, easy- flowing material.
In many cases, the design engineer may have to provide a larger area of bonded surface in his struc- ture so that the unit strengths can be reduced. But in the final analysis, any decision about the use of an adhesive, particularly for structural applications, must be qualified by a big IF- IFthe adhesive is properly used- IFthe adhesive bonds are properly prepared!
Processing and Quality Control
Members of the construction industry are not knowledgeable about adhesives and how to use them in structural applications. They are accus- tomed to using them for a wide variety of purposes where mistakes are easily rectified and failure of the adhesive bonds is not going to cause structural damage or loss of life. The industry lacks people with adequate technical training in this area. Be- cause of this, the adhesive supplier will have to supply not only his adhesive but a great deal of technical service- guidancein the use of his par- ticular adhesive. In many cases, he may have to develop a specific quality control program for his customer.
He will need to supply a variety of information about his adhesive: How is it affected by contami- nation of adherend surfaces? How it behaves in different glueline thicknesses? How it is affected by wood moisture content? How long an assembly time is either required or can be tolerated? How much pressure is required? How it responds to changes in different temperatures that migh occur either in the plant or on site? How much cure time must be allowed before the pressure is released or the assembly is moved? Failure to observe even one of these requirements of an adhesive system can often lead to disaster.
We have emphasized the problems faced by elastomeric construction adhesives when consid- ered for use in prime structural applications. This is the area requiring pioneering research. But de- velopments here can open up new markets for ad- hesives and can lead to more efficient use of building materials and thus reduce the drain on timber resources. These are all laudable objec- tives. It can be expected that other less critical uses for elastomeric adhesives in building construc- tion will continue to grow since they require less need for precise data on durability and mechanical properties.
Applications such as accessory and trim attach- ment involve traditional designs of structures and are not hampered by how fast innovations can be accepted by code agencies, lending institutions and consumers. Likewise, where adhesives simply pro- vide additional strength and stiffness to survive over-the-road hauling, where failure could be easily recognized and repaired or where failure would not affect life safety or loss of property, the oppor- tunities for immediate acceptance and use of elas- tomeric adhesives are bright.
Before elastomeric construction adhesives can be used to any great extent for prime structural appli- cations, a host of developments in a number of areas must take place. Progress here will depend upon how rapidly innovative and more efficient designs of composites can be accepted by regula- tory agencies and consumers. This will require de- velopments in test methods, generation of data, research by engineers and good communication between all parties concerned. Research and de- velopment work, and putting the results into prac- tice, is a lengthy and laborious process, particularly when it involves almost a revolution in a massive but highly fragmented industry.
The problem is complicated further by the fact that building practices and performance requirements differ in various regions in the United States. For example, snow loads are unimportant along the Gulf Coast, but wind resistance is of utmost concern. What is satisfactory for the arid South- west can be totally unsuitable for New England or the North Central region. It is the job of architects and design engineers to bring their expertise and judgment to bear on meeting specific performance needs in each specific case since adhesive require- ments depend not only upon the location within the building but also upon where the building is to be built.
Adhesives will have to be classified and de- scribed according to their engineering properties- data that architects and engineers can use in design and this is not the case today. Each design of a composite can involve a mixture of adherends, each with its own strength and stiffness properties. In assembling these different members, the bond- ing area can be quite large or quite small. This leads to widely different requirements when select- ing an adhesive to do the job. Architects and engi- neers will prefer to use a strong, rigid adhesive of proven performance because they can ignore its mechanical properties. A better understanding of what information architects and engineers will re- quire for new adhesive systems will be essential for progress to be made.
Summary
The attempt here has been to present a broad general picture of the use of adhesives in building construction with an emphasis on where elasto- meric construction adhesives might fit into the pic- ture. The picture is far from clear in many areas. There is a great need for research and development, and many facets of the problem are currently under investigation. Probably the greatest need is first to educate ourselves, then to educate those who need new information and new systems to provide improved housing and finally to educate the consumers as to the great benefits that can be derived from adhesive bonding in building construction.
